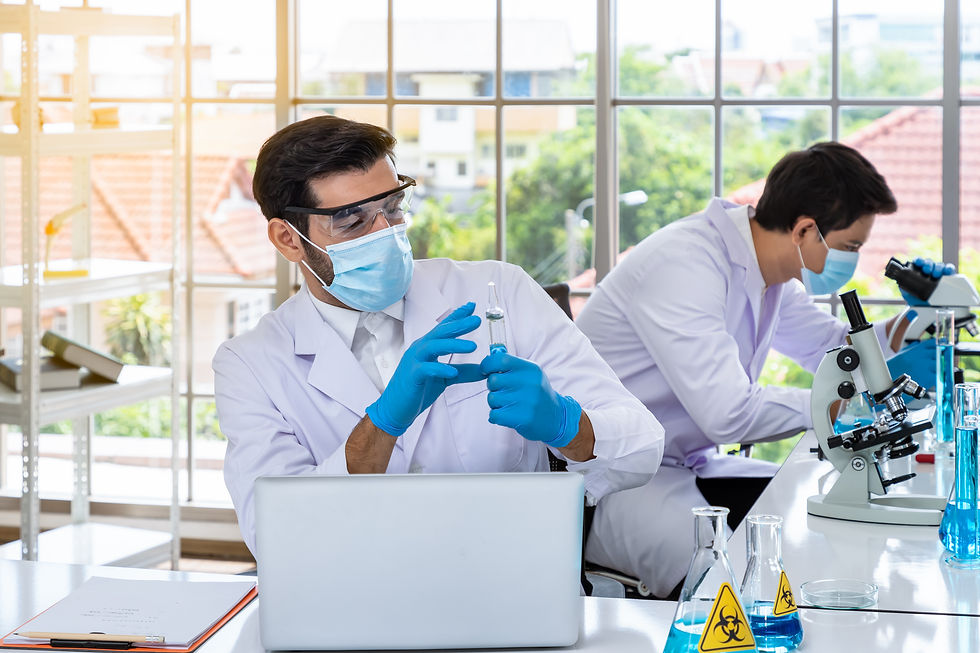
Background
Biopharmaceutical facilities are complex environments where precision and adherence to regulatory standards are crucial. In this case study, we explore the successful implementation of Commissioning, Qualification, and Validation (CQV) processes at a leading biopharmaceutical facility specializing in the production of therapeutic proteins.
Facility Overview
The facility, located in the United States, is a state-of-the-art plant equipped with advanced bioprocessing technologies. It has recently expanded its operations to include a new production line aimed at increasing its capacity to meet growing market demands. This expansion required a rigorous CQV implementation to ensure the facility's systems and processes met industry standards and regulatory requirements.
Objectives
Ensure Compliance: Achieve compliance with regulatory standards such as FDA 21 CFR Part 210 and 211, as well as international guidelines.
Enhance Operational Efficiency: Optimize the performance of new equipment and systems to improve production efficiency.
Reduce Risk: Minimize the risk of deviations and ensure the integrity of the final product.
CQV Implementation Process
Planning and Strategy Development
Initial Assessment: Conducted a comprehensive risk assessment to identify critical systems and components that required detailed scrutiny.
CQV Master Plan: Developed a CQV Master Plan outlining the scope, objectives, and timeline for the CQV activities. The plan also included roles and responsibilities, deliverables, and a detailed schedule.
Commissioning
System Installation Verification: Verified that the installation of new equipment and systems met design specifications and manufacturer’s requirements.
Operational Readiness: Conducted checks to ensure that systems were installed correctly, calibrated, and fully functional before the qualification phase.
Qualification
Design Qualification (DQ): Ensured that the design of the new equipment and systems met all user requirements and regulatory standards.
Installation Qualification (IQ): Verified that the installation of equipment and systems complied with the design specifications and was correctly installed.
Operational Qualification (OQ): Assessed the performance of the equipment and systems under operational conditions to ensure they functioned as intended.
Performance Qualification (PQ): Confirmed that the systems and equipment operated effectively under normal production conditions and met the required performance criteria.
Validation
Process Validation: Validated the new production processes to ensure they consistently produce products meeting quality specifications.
Document Review and Approval: Ensured all documentation related to CQV activities was thoroughly reviewed and approved. This included protocols, test results, and final reports.
Training and Knowledge Transfer
Staff Training: Conducted training sessions for staff on new equipment and processes, emphasizing best practices and compliance requirements.
Knowledge Transfer: Facilitated knowledge transfer sessions to ensure that the operational and maintenance teams were well-informed about the new systems.
Continuous Improvement
Monitoring and Support: Implemented a monitoring system to track the performance of the new systems and address any issues promptly.
Feedback Loop: Established a feedback mechanism to capture lessons learned and identify opportunities for further improvements.
Results
Regulatory Compliance: The facility successfully achieved compliance with all relevant regulatory standards, including FDA and international guidelines.
Operational Efficiency: The new production line significantly enhanced operational efficiency, leading to a 20% increase in production capacity.
Risk Reduction: The comprehensive CQV approach minimized the risk of deviations and ensured the integrity and quality of the final product.
Challenges and Solutions
Challenge: Delays in equipment delivery impacted the project timeline.
Solution: Adjusted the CQV schedule to accommodate the delays and prioritized critical systems to stay on track.
Challenge: Training staff on new processes required additional time and resources.
Solution: Developed a detailed training program and provided additional resources to expedite the training process.
Conclusion
The successful implementation of CQV processes at this biopharmaceutical facility demonstrated the importance of thorough planning, execution, and ongoing support. By adhering to a structured CQV approach, the facility not only ensured regulatory compliance but also enhanced operational efficiency and product quality. This case study serves as a valuable reference for other biopharmaceutical companies undertaking similar projects.
Comments